Torpado Technologies




CARBON FIBER
Used fibres are T700, T800, TR50S, MR50 and Hr50; all these fibres have unidirectional finish. All linkage areas have a directional reinforcement with 3K carbon to guarantee stiffness and performances.
DESIGNED FOR PERFORMANCE
Each part of the frame has been designed to guarantee better performance. We used the FEA (Finite Element Analysis) software to simulate the modalities while solicitations are present. This operation has permitted us to develop the best disposition and the use of the carbon fibres.

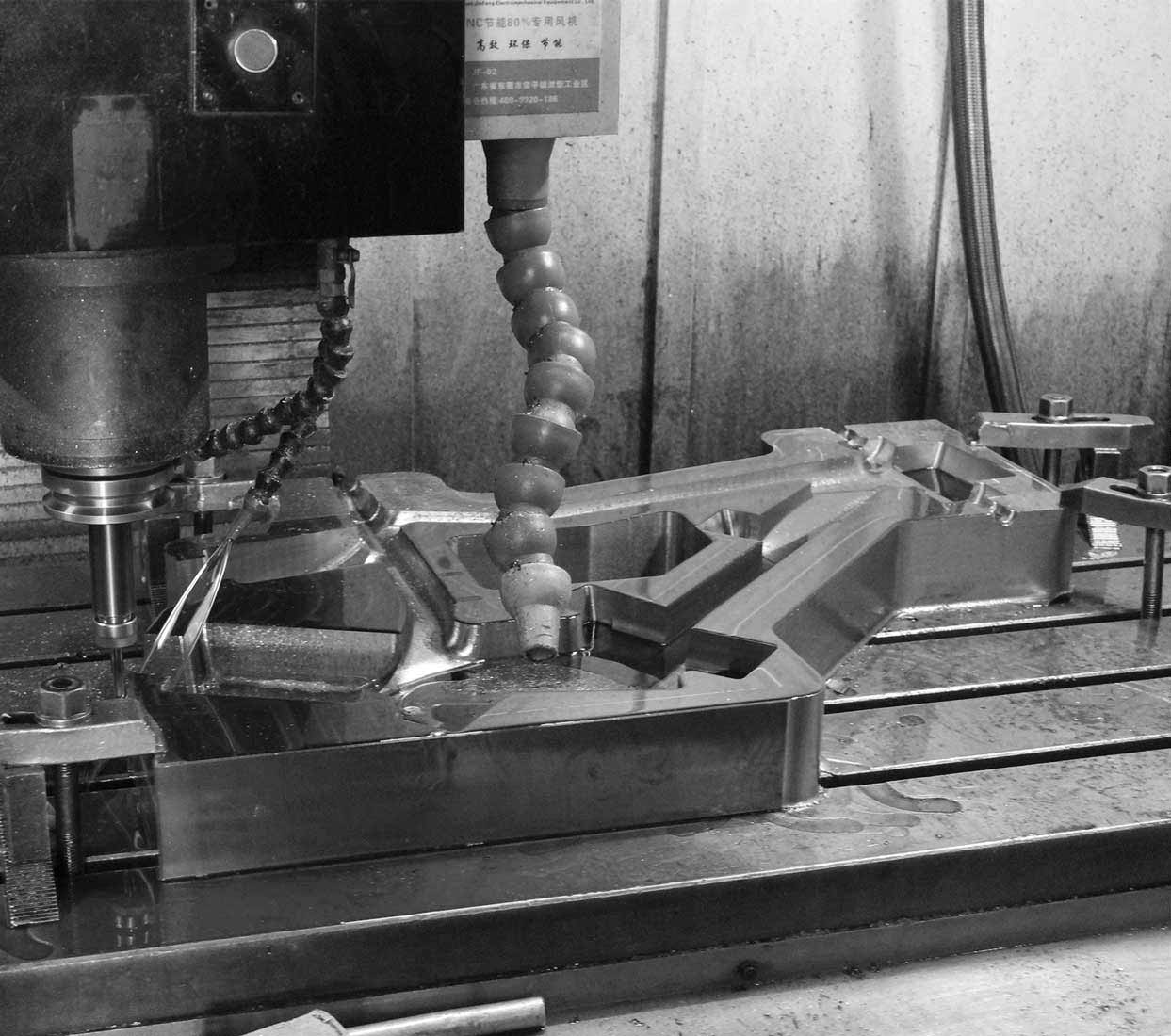


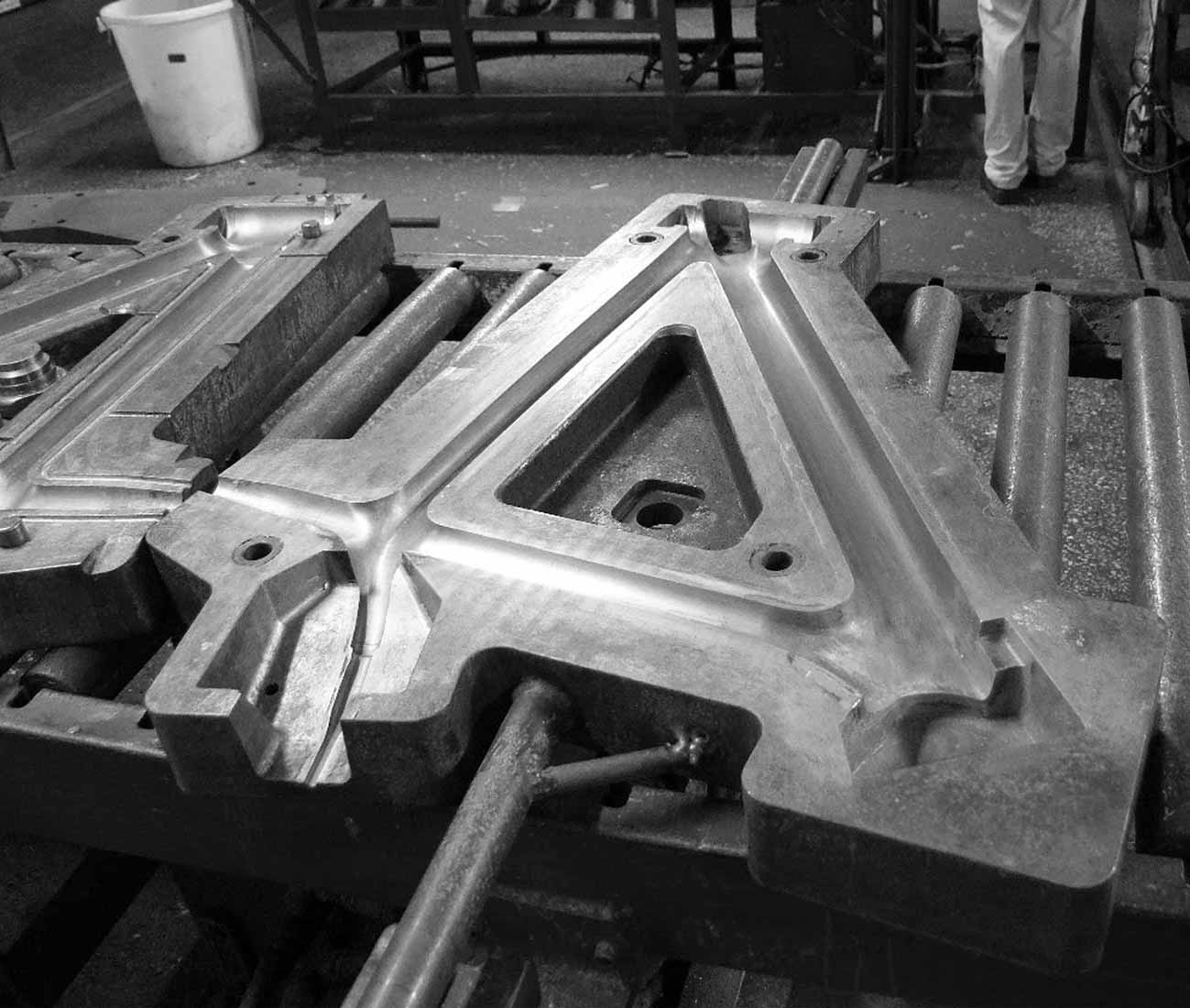

PRE-PREG
Pre-preg is the process, which consists of directional and unidirectional Carbon fibers impregnated with resin during the production process. Then, pre-preg carbon fibre is placed on a mandrel before being inserted in a pre-warmed monocoque mold. During the warming-up process, epoxy resin flows through the different layers: such action creates a compact structure, which confers to the frame its own shape and peculiarities in terms of performance.
EPS PRODUCTIVE PROCESSES
We use mandrels built in polyurethane expanded / polystyrene expanded (PU / EPS) in key areas as BB, dropout, head tube, seat tube and chain stays. We pay a lot of attention to the thickness of the tubes to satisfy the tolerances in terms of dimension, alignment and resistance in relation to the load. This technology allows us to reduce the slags inside to the frame and to achieve a more regular and lighter surface.

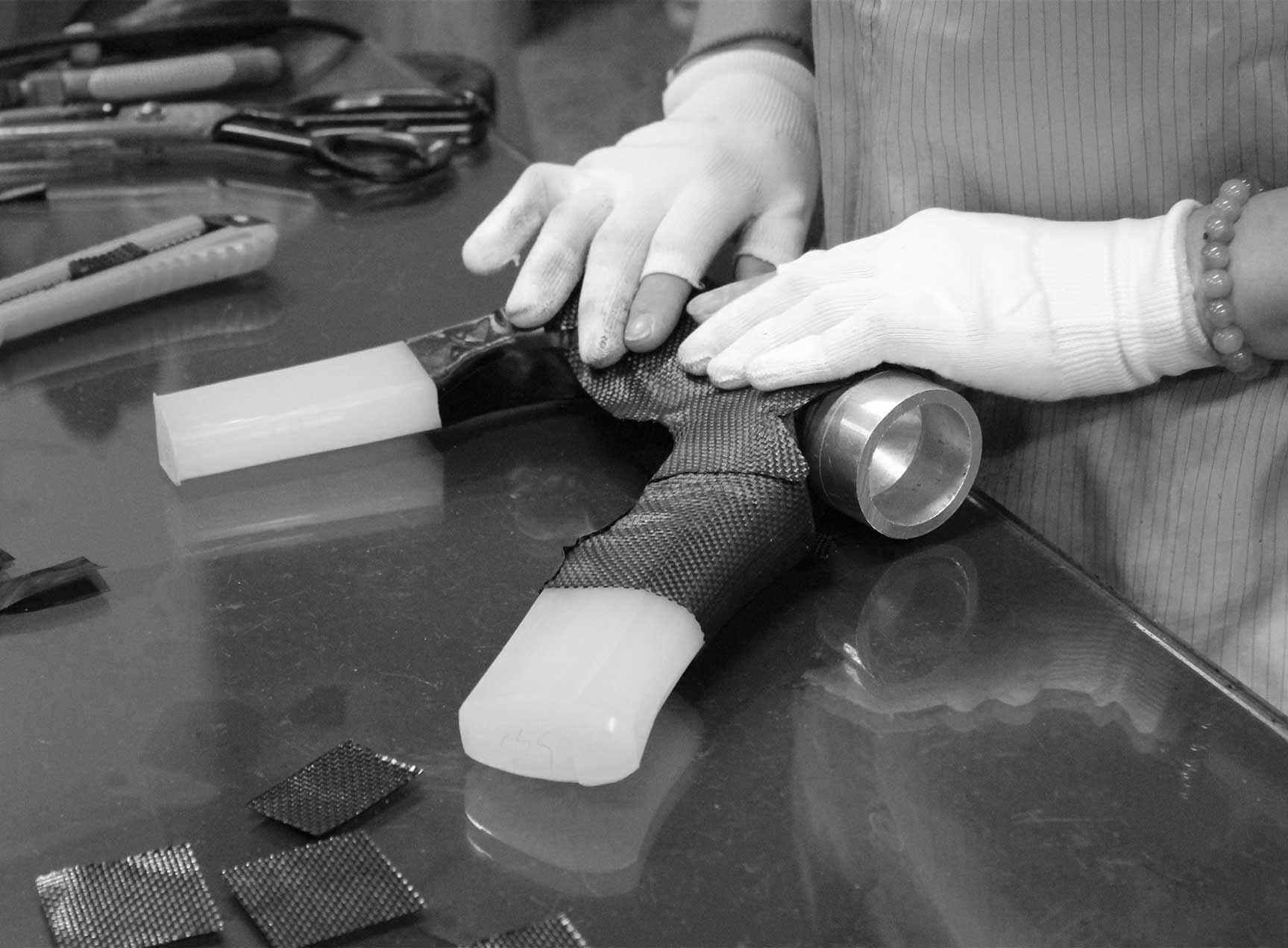


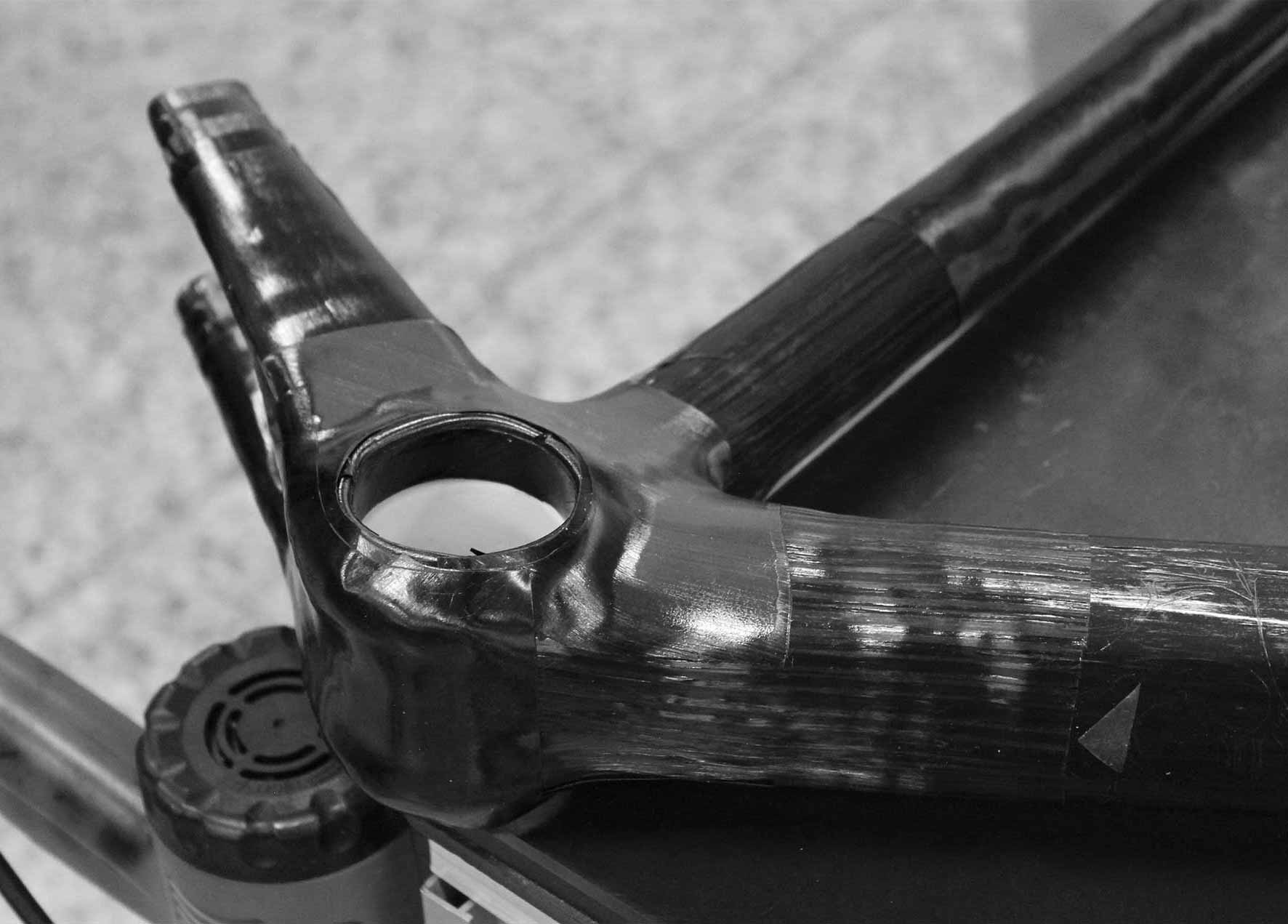

The carbon is a composite material. It’s perfect to produce light frames with the ability to perform. The everlasting evolution on productive process contributes to the development of technology, which allows for features that improve day by day. Torpado builds different product lines, which differentiate from one another because of the use of different fibres and different technologies. As you can see below on Fig.1, carbon fibers have different features based on the following factors:
- Number of fibres;
- Resistance to traction;
- Tensil modulus;
- Lengthening;
- Mass per unit of length;
- Density.
The lamination and orientation and the use of different typologies of fibres, paired with different productive processes, allows us to realize the different products’ line, with different features of weight (thickness) and behaviour (stiffness – elasticity) These variables cause the lines:
- X (0,9 mm)
- S (1,05 mm)
- N (1,2 mm)
The X line has an exceptional relationship between weight and mechanical behaviour. X is the “Extreme” line and it provides for the use of more performing materials and more profitable production technologies.

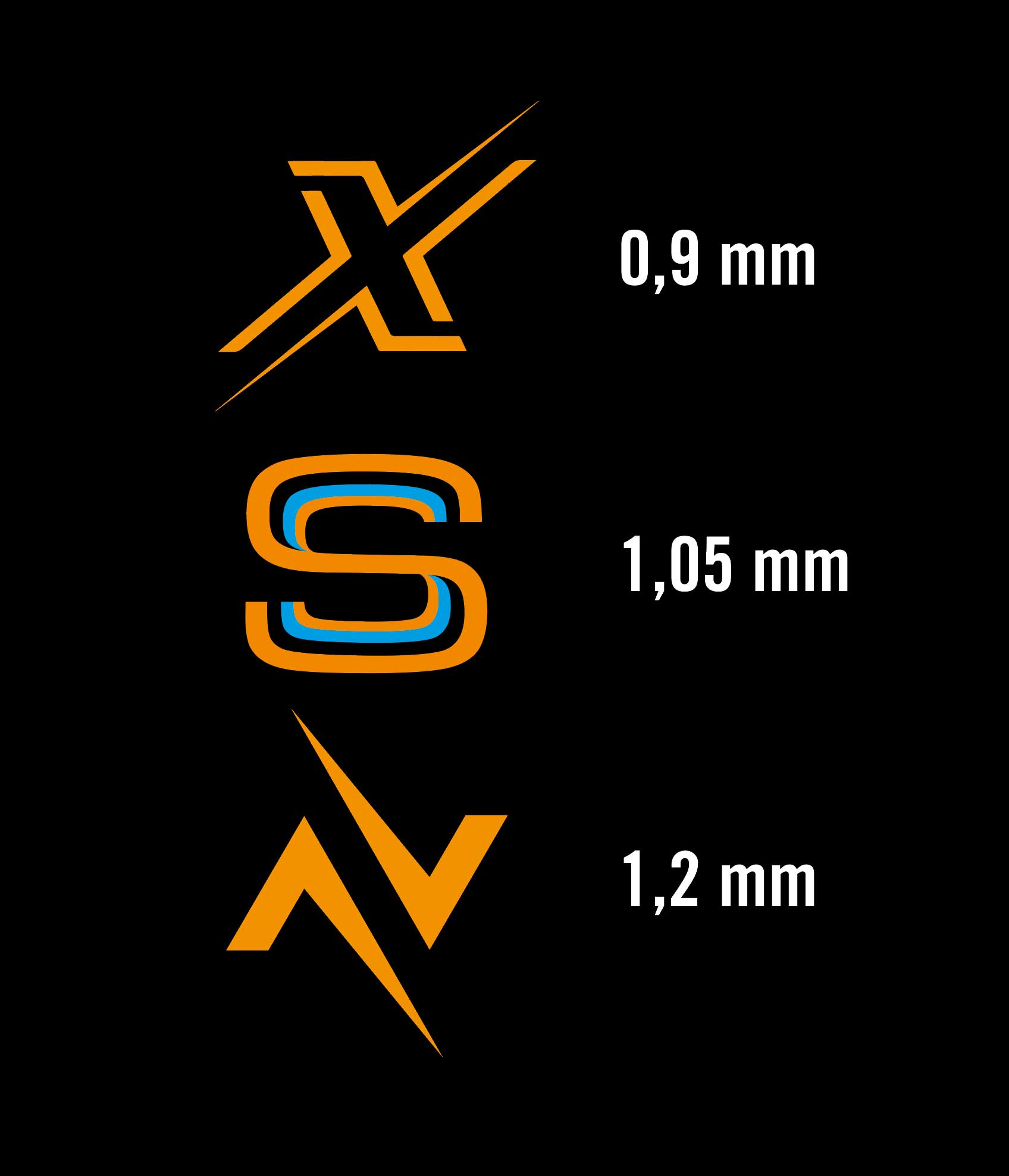

How are Torpado bicycles born? Discover our technologies and the materials we use to make our products.